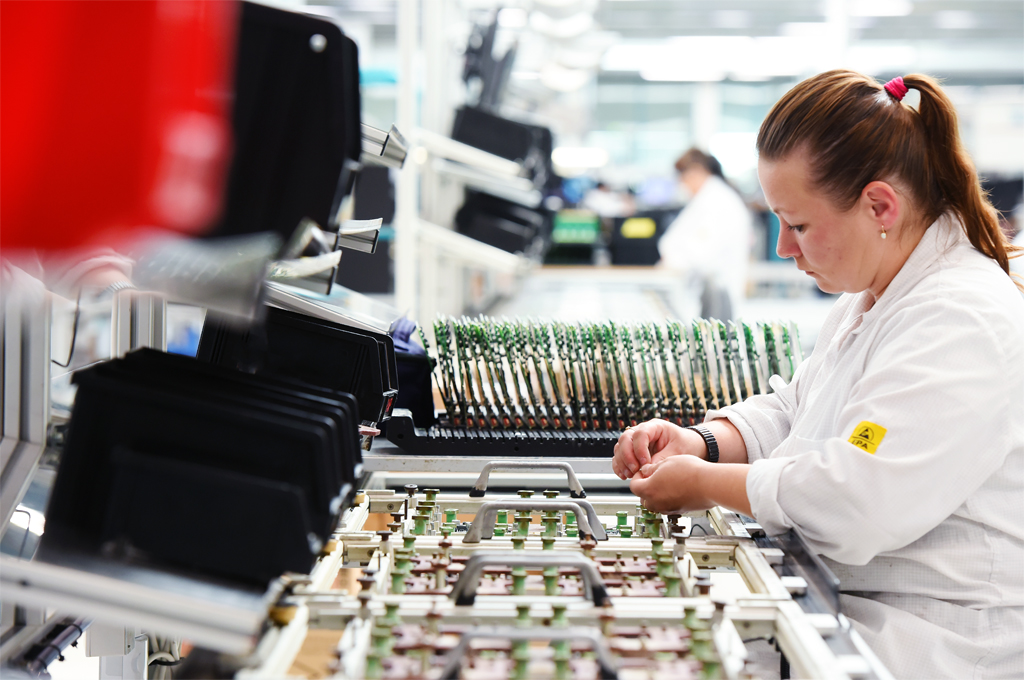
In the fast-paced world of electronics, where innovation knows no bounds, Printed Circuit Boards (PCBs) stand as the unassuming but indispensable linchpin. These vital components form the foundation of nearly all electronic devices, from smartphones to laptops, medical equipment, and even space exploration technology. pcb assembly fabrication is a sophisticated and intricate process that plays a pivotal role in shaping the devices we rely on daily.
PCB fabrication begins with the design phase, where engineers meticulously plan the layout of components and routes for electrical connections. This design, often created using specialized software, determines the board’s functionality, size, and overall structure. The precision of this step is crucial as any errors or oversights can lead to costly and time-consuming rework later in the process.
Once the design is complete, it’s time to select the right materials. Most PCBs consist of multiple layers of substrate material, typically fiberglass-reinforced epoxy, with copper sheets bonded to them. These materials are chosen for their electrical properties, durability, and ability to withstand a range of environmental conditions. Manufacturers must select the appropriate thickness and copper weight to meet the specific requirements of the PCB.
With the design and materials in place, the next step is to fabricate the PCB. This is achieved through a complex series of processes, primarily involving etching and drilling. Copper sheets are laminated onto the substrate and then coated with a photosensitive layer. The design pattern is transferred onto the board, and the unwanted copper is etched away, leaving behind the circuit traces. Precision is paramount here, as the tiniest miscalculation can render the board useless.