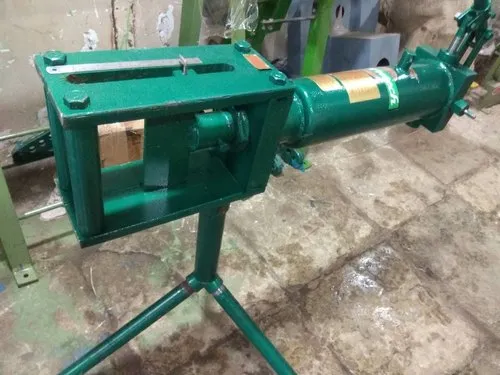
In the ever-evolving landscape of modern manufacturing, the introduction of advanced technologies has reshaped industries and elevated production processes to new heights. Among these groundbreaking innovations, the busbar machine stands as a pinnacle of precision, power, and efficiency. With the ability to transform raw materials into intricate shapes and designs, these machines have revolutionized the way products are created across a multitude of sectors.
Bending machines, often referred to as press brakes, are a cornerstone in the metalworking realm, playing an indispensable role in shaping various materials like steel, aluminum, and other metals. These machines leverage a combination of force, precision hydraulics, and computerized controls to manipulate metal sheets into intricate forms, angles, and bends with remarkable accuracy. What sets bending machines apart is their capacity to deliver consistent results over large volumes, saving both time and resources while maintaining exceptional quality.
One of the most striking aspects of bending machines is their versatility. From automotive components and aerospace parts to architectural elements and consumer goods, bending machines find applications in diverse industries. The ability to create complex shapes and configurations has enabled engineers and designers to push the boundaries of what was once thought possible, resulting in more innovative and efficient product designs.
Furthermore, bending machines have significantly reduced the need for manual labor, minimizing the risk of errors and ensuring worker safety. The incorporation of advanced software and computerized controls has led to enhanced automation and streamlined operations, allowing manufacturers to meet tight production deadlines without compromising on precision. This level of automation not only increases overall efficiency but also offers businesses a competitive edge in a fast-paced market.